Industrial masking tape is a cornerstone in various sectors, acting as a versatile tool for diverse applications that demand precision, reliability, and efficiency. Drawing from years of field experience and expertise, this article delves into the intricacies of industrial masking tape, illustrating its significance, applications, and the factors contributing to its indispensability in professional environments.
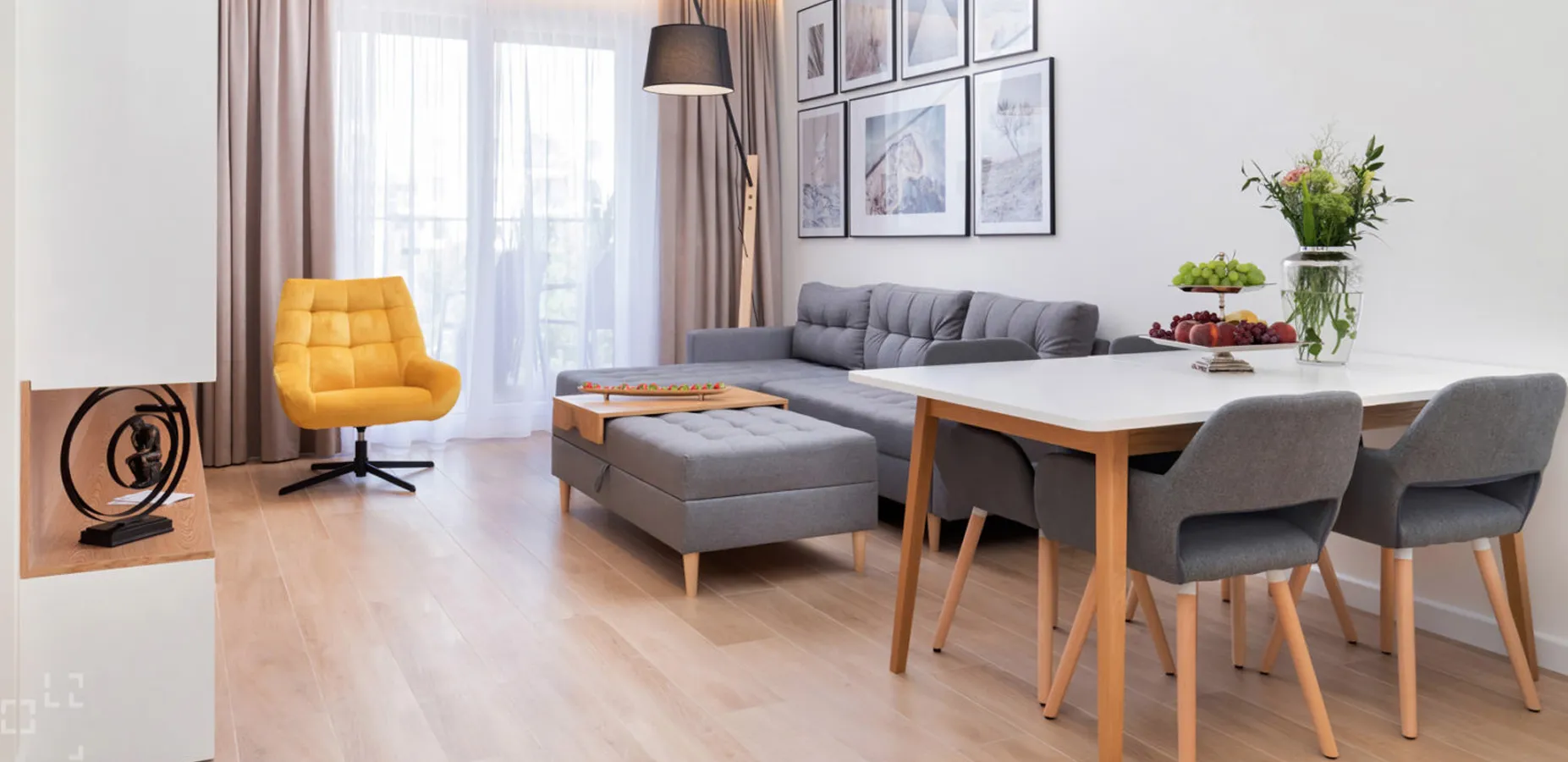
Industrial masking tape, unlike its domestic counterpart, is engineered with superior adhesive properties and high-temperature resistance to withstand demanding conditions. This class of tape plays vital roles in industries such as automotive, aerospace, construction, and manufacturing. For instance, in automotive painting, masking tape is crucial for achieving clean, crisp edges, ensuring that intricate designs are flawlessly executed without bleeding or smudging. The high-temperature variants can endure the heat from curing ovens, highlighting their ability to maintain performance standards under rigorous conditions.
In aerospace, where precision is paramount, masking tape is employed not only for painting but also during assembly processes to protect components from damage. This application demands a tape that can adhere strongly without leaving any residue upon removal—failure to do so could compromise part functionality or require costly rework, emphasizing the need for tapes that adhere to stringent industry standards.
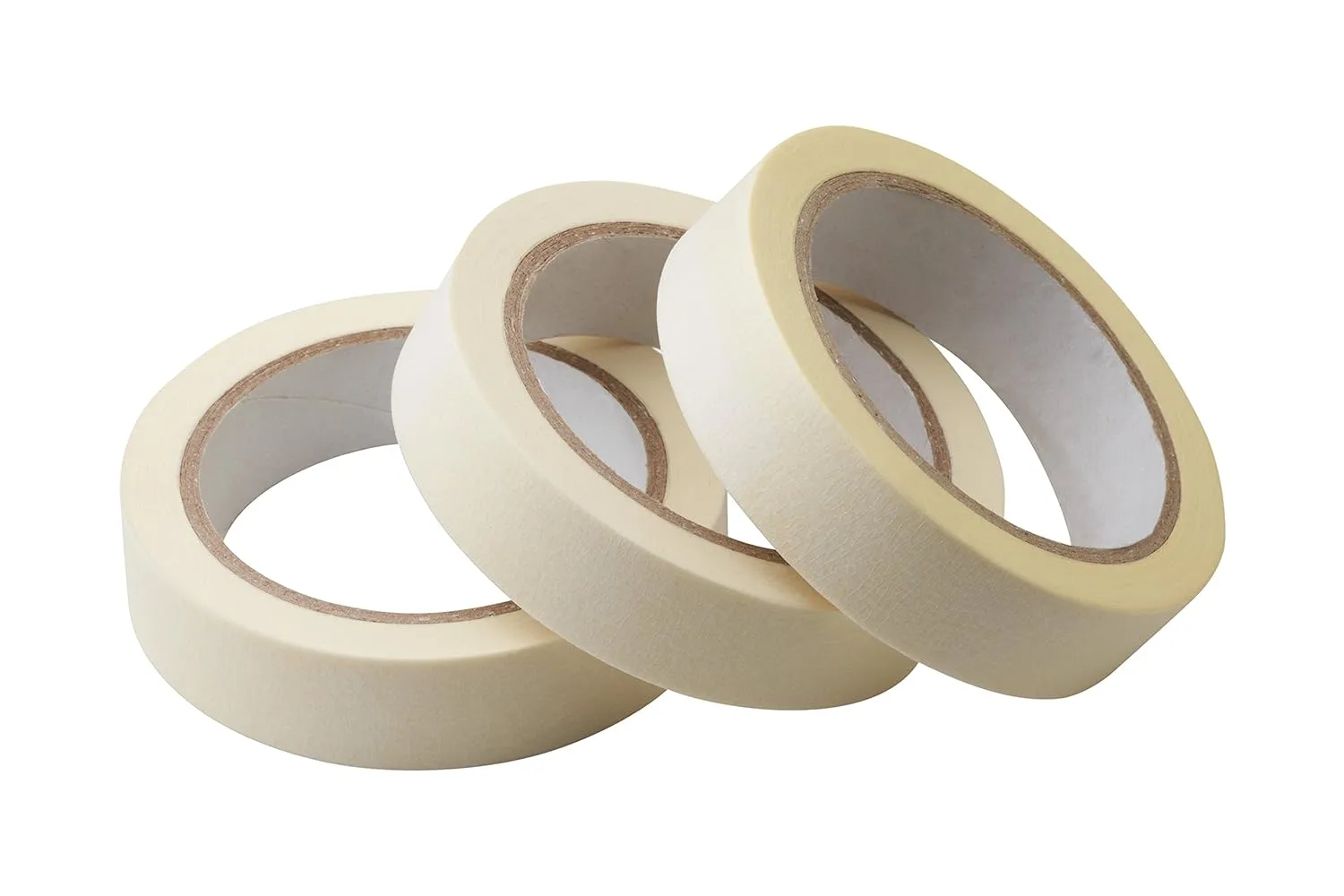
Construction and manufacturing sectors frequently rely on industrial masking tape for its versatility and ease of use. In construction, it provides temporary protection to surfaces during welding, cutting, or painting, ensuring that surfaces remain pristine. Manufacturing processes utilize masking tape as part of their lean approaches, helping streamline workflow by marking areas, bundling items, and protecting parts, thus maintaining organization and efficiency within production lines.
masking tape industrial
The expertise in choosing the right masking tape is crucial. Factors such as adhesive strength, heat resistance, material compatibility, and environmental conditions must be considered. The development of different types of adhesives and backing materials allows manufacturers to offer a variety of tapes tailored to specific applications. Silicone adhesives, for example, are known for their excellent heat resistance and are often used in high-temperature environments, while rubber adhesives provide superior initial tackiness for projects requiring strong immediate adhesion.
Authority in the masking tape industry is often demonstrated by compliance with certifications and standards such as ISO 9001, which assures quality and consistency in product manufacturing. Brands that consistently meet or exceed these standards earn a reputation of reliability and trust, providing customers with peace of mind knowing they are investing in products that deliver consistent performance.
Trustworthiness in industrial masking tape applications is built through rigorous testing and real-world use cases. Feedback from industry professionals and extensive testing processes ensure that the product not only performs as expected but also exceeds established benchmarks. This dedication to maintaining high standards reinforces customer confidence and establishes a brand as a leader in the industry.
In summary, industrial masking tape is an essential component in numerous professional environments. Its adaptability, combined with superior adhesive properties and resistance to challenging conditions, makes it a preferred choice across multiple industries. Knowledgeable selection of the appropriate masking tape, coupled with an understanding of its standardized performance and reliability, ensures optimal results and reinforces its role as an invaluable tool in industrial applications.