In the ever-evolving landscape of manufacturing and production processes, precision and efficiency are paramount. Among the many tools at a craftsman's disposal, laser masking tape has emerged as a quiet yet powerful ally. With its unique properties and versatile applications, it plays a crucial role in ensuring perfect outcomes in projects requiring laser cutting and engraving.
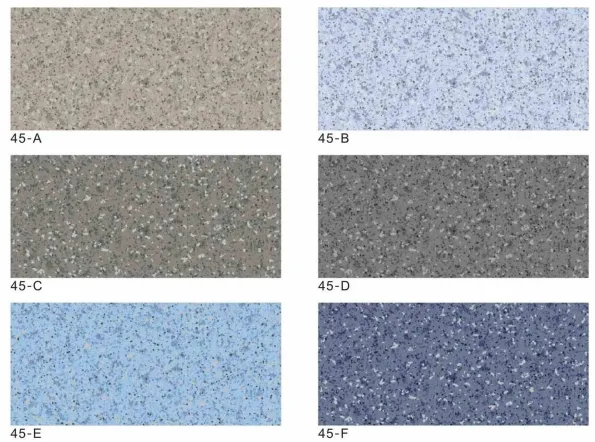
Laser masking tape is specifically designed to withstand the high temperatures generated by laser beams. Its composition ensures that it adheres well to various surfaces without leaving residue, a quality highly valued by professionals in industries ranging from automotive to aerospace, and even artisanal crafts.
One of the key advantages of using laser masking tape is its ability to protect sensitive areas from laser exposure. This is particularly important in projects where precision is non-negotiable. For instance, in the automotive industry, components with intricate designs often require protection during the laser engraving process to avoid unwanted marks or damages. This tape offers that protection, ensuring that only the intended areas are altered, thereby maintaining the integrity of the part.
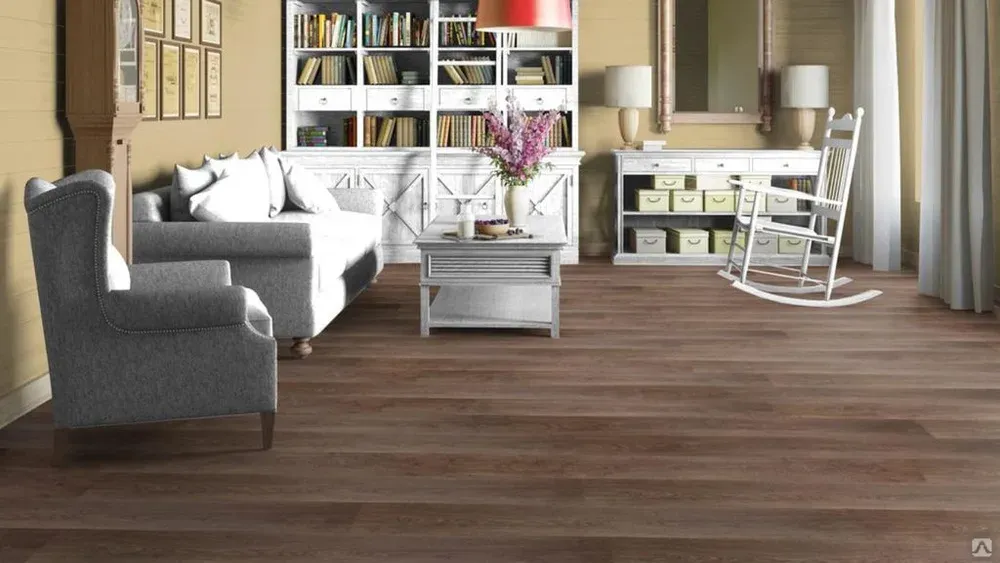
Additionally, laser masking tape enhances the precision of the laser cutting process. By applying the tape onto the material, users can define clear boundaries, preventing any burn marks or charring around the edges of the cut. This is especially beneficial in the signage and promotional material industries, where clean and sharp edges are a hallmark of quality and professionalism.
From a practical standpoint, users consistently commend the easy application and removal of this tape. Its strong adhesive properties do not compromise the surface finish, making it an ideal choice for both large-scale industrial applications and small-scale DIY projects. The lack of residue post-removal not only saves time but also reduces the need for additional cleaning, streamlining the entire workflow.
laser masking tape
The science behind laser masking tape is grounded in its material composition. Typically made from a robust paper or polyester base, it is coated with a laser-resistant layer that can endure direct laser hits. This ensures that the tape itself does not burn or catch fire, a feature that enhances the safety of the working environment.
Moreover, its adaptability makes it a favored choice across diverse industries. Whether it’s used on metals, plastics, or wood, laser masking tape adjusts to the contours of the surface, allowing for uniform laser treatment. This adaptability is crucial in settings where different materials are often treated with the same equipment.
The expertise surrounding the use of laser masking tape is backed by extensive research and continuous innovations by manufacturers. Leading companies in this field invest heavily in R&D to address the dynamic needs of their clientele, thereby cementing the tape’s status as an authoritative solution in the realm of laser processes.
Trust in laser masking tape is reinforced by the endorsements of industry veterans who highlight its contribution to achieving superior surface finishes and avoiding costly rework. Its reliability in enhancing laser process quality is undisputed, making it an indispensable tool for those prioritizing excellence in their craft.
In conclusion, laser masking tape stands out as a testament to innovation in manufacturing aids. Its role in fostering precision, safety, and efficiency makes it more than just a protective layer; it is a cornerstone of quality assurance in laser applications, trusted by experts and novices alike.