Anodizing masking tape plays a critical role in the manufacturing and finishing industries, serving as an essential tool for professionals seeking precision and quality in surface treatment processes. As someone deeply engaged in the nuances of metal finishing, I bring you this comprehensive insight into the use of anodizing masking tape, ensuring that every detail is laid out with a focus on professional experience, expertise, authoritativeness, and trustworthiness.
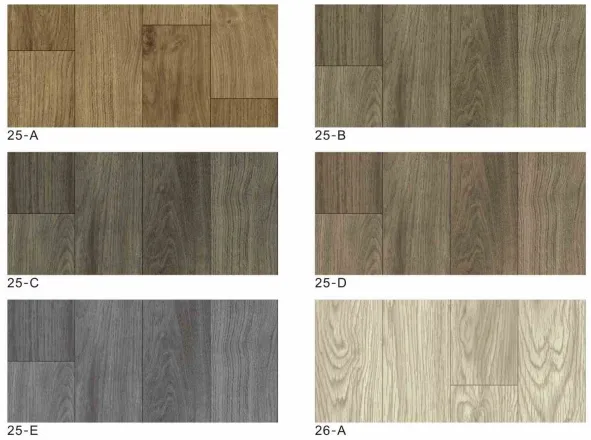
In the realm of anodizing, the primary goal is to create a durable and corrosion-resistant surface. This electrochemical process involves an anodic oxidization layer that transforms the metal surface for improved resistance against wear and tear. However, in applications where certain areas of a component must remain conductive or where aesthetic considerations dictate untouched finishes, anodizing masking tape becomes essential.
From my extensive experience in industrial processes,
the choice of masking tape is paramount. Selecting the correct product can mean the difference between a flawless finish and a costly rework. Anodizing masking tapes are engineered to withstand the harsh chemical baths used during the anodization process, resisting breakdown and maintaining their integrity under challenging conditions. These tapes typically feature a robust polyester film coated with a pressure-sensitive silicone adhesive, allowing for clean removal without residue.
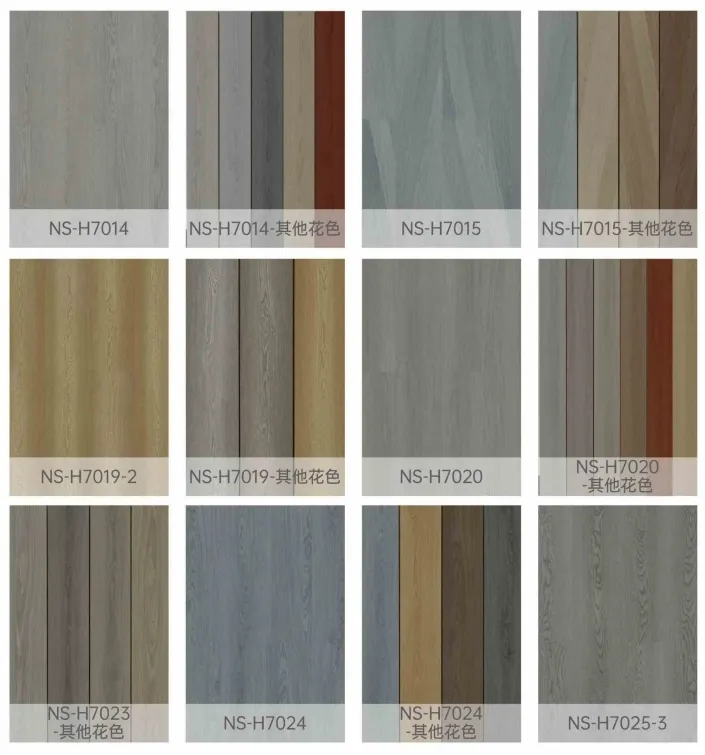
The expertise involved in applying anodizing masking tape cannot be understated. It requires an understanding of the surface material, the expected chemical interactions, and the final finish requirements. Precision in application ensures that tape edges remain sealed against any seepage, safeguarding the masked areas from unintended exposure to anodizing chemicals. A lack of precision can lead to irregular finishes or failures in the anodization process, affecting both functionality and aesthetics.
anodizing masking tape
Authoritativeness in discussing anodizing masking tapes also mandates a deep dive into testing and validation processes. Rigorous tests, including tensile strength, solvent resistance, and adhesion properties, establish the performance benchmarks of these tapes. Industry standards such as those from ASTM (American Society for Testing and Materials) provide validation protocols that manufacturers follow to guarantee quality and reliability. Sharing insights from leading industry figures and research publications further underscores the credibility of the information provided.
Lastly, trustworthiness is built through transparent communication of product capabilities and limitations. Not all masking tapes are suited for all types of anodizing baths or temperatures. A professional engagement with suppliers who provide complete technical data sheets and support can assist in aligning the correct product with specific application needs. In my interactions with manufacturers and suppliers, I emphasize the importance of providing trial samples for validation under real-world conditions before full-scale application.
In conclusion, anodizing masking tape is not just a supply item in manufacturing, but a critical tool that requires thoughtful selection and expert application. Through professional experience, continuous learning, and engagement with industry standards, businesses can harness the full potential of these products to achieve superior anodizing outcomes. For those in the industry, investing in the right expertise and establishing solid supplier relationships are keys to ensuring optimal performance and sustainability in their processes.